One of the most popular applications in laser measurement are laser diffraction measurements. This technique uses telecentric laser beams (that means beams with minimal divergence such as the Laser Diode Collimators Flatbeam®) and can e.g. be used to evaluate the diameter of an object by analyzing the Fresnel diffraction pattern of the shadow edge. The flat wave front emanating from the colllimator is bent by the object and the diffracted light perturbs the integrity of the shadow cast by the object, with the diffraction patterns arising from interference between the distorted and undistorted light beams. A line sensor detects the single or multiple Fresnel diffraction shadows directly and without any temporary image storage.
Laser diffraction measurements
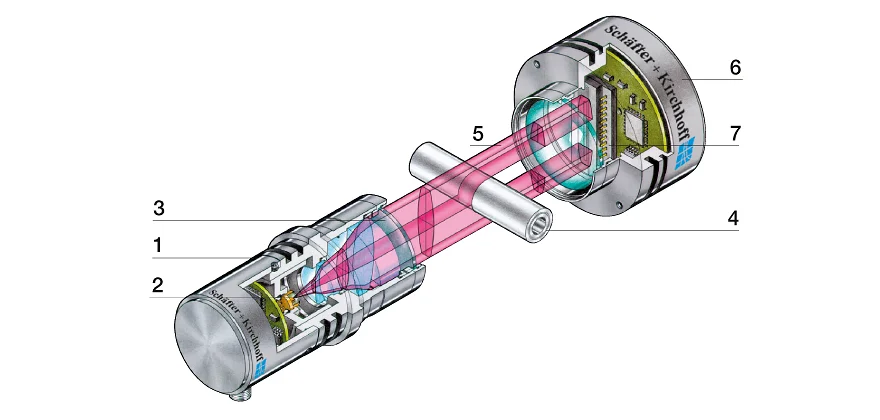
Setup
Schematic laser diffraction measurement and illumination.
The collimated beam is elliptical (beam height = 32 mm).
1 Laser diode collimator
2 Laser diode
3 Lens for collimation of the divergent laser diode beam
object to be measured
4 Object
5 Partially blocked laser beam
6 Line scan camera
7 Line sensor
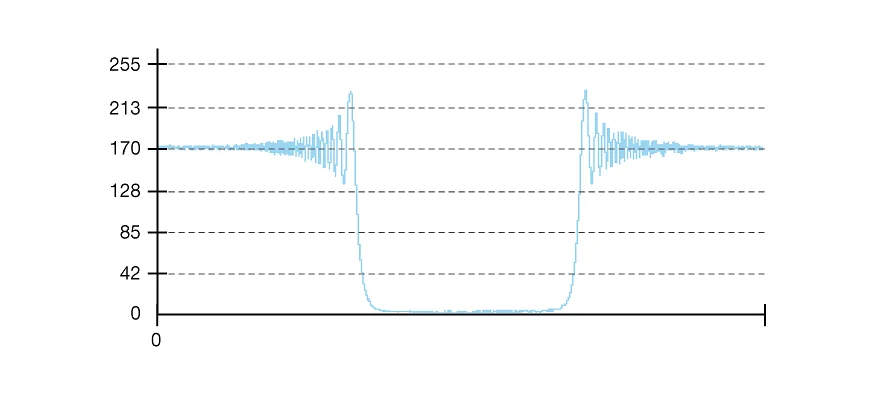
Fresnel pattern
Characteristic Fresnel diffraction patterns of the measured object captured by the line sensor.
Shadow edge analysis
The shadow edge can be determined using two different ways - depending on the speed and accuracy required.
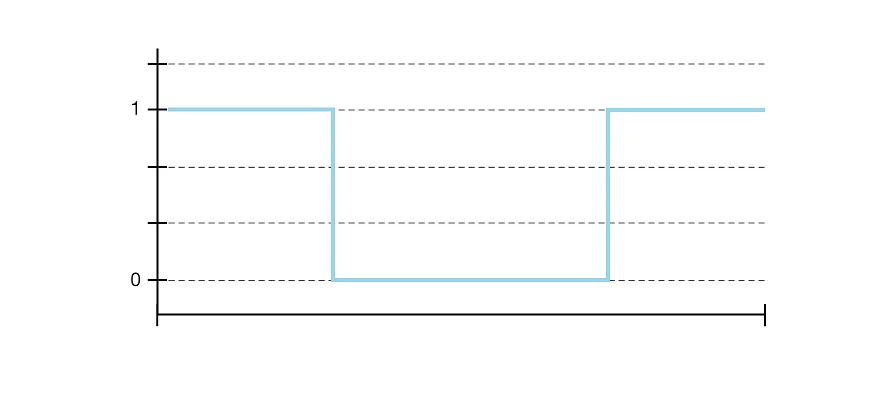
Thresholding
With thresholding, the complexity of the diffraction pattern is ignored and the line scan camera signal is simply reduced to a binary output which shows the pixel position of the shadow edge. Measurement frequencies of over 30 kHz can be achieved at accuracies below 7 µm.
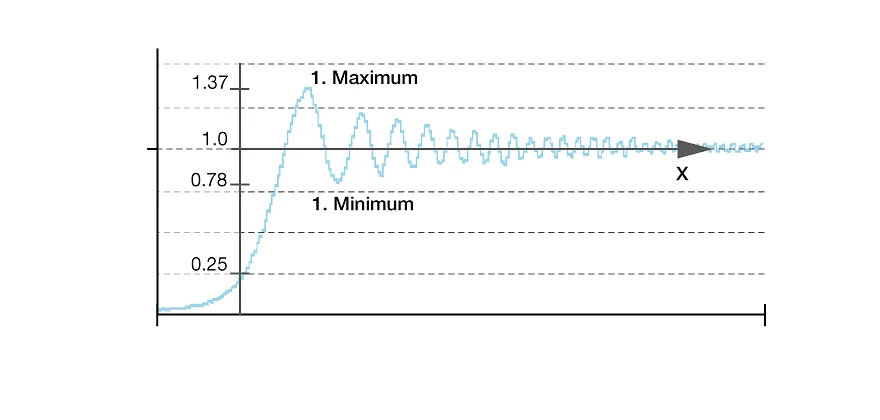
Laser diffraction method using the Frsenel pattern
The laser diffraction method uses the oscillating area of the Fresnel interference patterns. Evaluation of the position and the intensities of the minima and maxima leades to a precise measurement of the edge position with a resolution < 1 µm. Additionally, the interference patterns at a defined wavelength can also provide information about the precise distance between the measured object and the line sensor.
The computational demands of laser diffraction evaluation are high and restrict the available measuring frequency in comparison with thresholding.